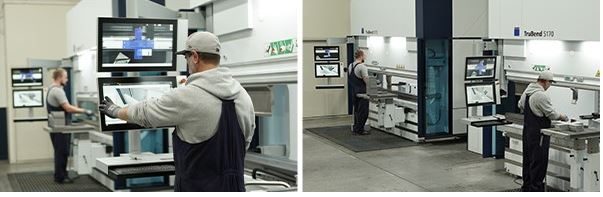
Mulcahy provides end to end processing solution
With the addition of two new Trumpf TruBend 5170s to their bending operation, Auckland-based Mulcahy Engineering can provide customers with a complete end-to-end processing solution.
“The technology associated with the new machines allow us to take the customer’s model and carry it right to the finished folded part with complete accuracy, using innovation such as TechZone bend offline programming software,” managing director Kayne Mulcahy explains.
The software takes the customer’s model for a product or component and generates a press programme for it at the order processing stage.
“This minimises the risk of human error and vastly improves process efficiency,” says Kayne.
Once at the machine, the operator refers to an augmented reality view of the part they’re folding on-screen to ensure everything is aligned and folded the correct way.
A Laser Automatically Controlled Bending (ACB) device measures the folded angle in real time, adjusting the pressing force to ensure 100% accuracy of the fold, every time.
Additional Industry 4.0 initiatives allow real time monitoring of press performance through Machine Data Analytics (MDA). And thanks to the 6 axis back gauge, products with even asymmetrical geometry can be folded with 100% accuracy.
“We’ve always been committed to enabling our customers to be innovative,” Kayne says.
Investing in not one, but two new Trumpf TruBend 5170s is a further demonstration of this commitment.
“The accuracy achieved through the new technology means faster speed of delivery and greater flexibility, all of which adds up to greater efficiency for our customers.”
Mulcahy Engineering operates six press brake machines at their Auckland premises, with up to 230 tonne capacity and 4.25m press length.
Let’s talk about how our accurate and efficient end to end processing can work for you.